Mastering History
from the tape to the lathe.
volumes
vol. 1
Mono Masters
(1955 to 1958)
vol. 2
Peak Contemporary
(1958 to 1966)
vol. 3
Tone Changes
(1966 to 1984)
vol. 4
Idiosyncrasies of the Sound (1984+)

back in 1955,
Roy DuNann was still the studio manager at Capitol Studios in Hollywood.
Lester Koenig was a producer who contracted Capitol’s space and services for Good Time Jazz dates. Roy remembered — fifty years later⁽¹⁾ — Koenig’s “fussy” attention to sound quality which saw him schlepping his own case of European microphones to each and every session.
Perhaps Les grew tired of the runaround, particularly with his Contemporary Records offshoot picking up steam in the 12-inch LP market, and it’s around this time he began laying plans to build his own studio. This meant hiring an engineer to lead the technical build-out and manage the facility full-time.
Roy, who’d begun to feel the pains of Capitol’s corporate structure⁽¹⁾, happily took the job.
Building a recording space served multiple drives for Koenig, “one being the obvious economy of not having to hire expensive studio space” and “two, the natural acoustics” of his existing office’s stockroom at 8481 Melrose Place⁽²⁾. Lester was both a shrewd businessman and committed audiophile, and both of those personas valued vertical ownership over sound.
It may have been a nag that disc mastering remained outside his purview (for now), but the engineers and equipment at Capitol remained stellar. In the now-mythical Thomas Conrad profile The Search for Roy DuNann, Roy recalled that Lester considered Capitol “the best mastering facility” in the region. Capitol, thus, cut all 12-inch Contemporary lacquers from 1955 to 1957.
Capitol Studios, 5515 Melrose Ave.
The Billboard, May 5, 1956
1750 Vine St, on film. Looks the same today.
Mastering, Lacquers, and Lathes
Stepping back, let’s define some terminology. The word mastering became murky with the growth of digital audio in the 1980s, but when speaking to the pre-digital era when vinyl was king, mastering meant cutting a disc master.
That disc is more specifically called a lacquer. It’s a round piece of aluminum coated with a thin, smooth layer of soft nitrocellulose. Once etched with musical grooves this is what gets handed off to plating and pressing folks who translate it into vinyl.
How exactly does it get etched with music? This involves a cutting engineer using a chain of electronics we’ll call, collectively, the cutting system. At it's apex are the cutting lathe, cutting head, and cutting amplifier(s).
The cutting lathe is a metal beast consisting of 1) a turntable and drive mechanism to spin the disc at constant speed, 2) a carriage which holds a cutting head, and 3) a leadscrew which moves the carriage & cutterhead over the disk as it spins. Critical to its function is automatic control of the leadscrew motor (aka pitch control, which we’ll discuss in Chapter 2.)
The cutting head is what it sounds like, a housing for the coil (two coils, for stereo) and stylus which cut the signal into the master disc.
Moving backwards along the cable(s) feeding signal to the cutting head, you’ll find the cutting amplifier(s). Imagine each coil inside the cutting head is a little speaker; the cutting amp is what drives that coil. It delivers the power necessary to faithfully translate the electrical musical signal to a physical expression.
Neumann lathe and cutting head in action.
Add in a source component — let’s say a tape machine — and what we’ve just discussed are all that’s strictly necessary in a cutting system. A simple path — tape machine, amp, lathe, cutterhead — with little room or need for operator input. Such was the nature of many cutting systems back in the 1950s.
However with the evolution of “high fidelity” sound and the introduction of stereo LPs in the late 1950s came new cutting challenges. Soon after this, multitrack mixing expanded the limits of recording, one side effect of which was more uneven masters track-to-track and up and down the frequency spectrum. Quickly the cutting stage became burdened with tweaking and tailoring sound so it could be properly transferred to disc on a subjective level.
This required flexibility, so the space between source and amplifier swelled with equalizers, limiters, compressors, de-essers, and more. As these tools became necessary components in any engineer’s toolbox, the cutting job changed form. Engineer became artisan.
Meanwhile the proliferation of outboard spokes obligated a complex nexus to control them: the mastering console. You’ve seen lots of consoles; it’s that wide, low-grade deck that mastering engineers sit at in videos. Back in the late 1950s, early consoles would have been rackmount situations, vertical in nature, and the knobs fewer in number.
a Scully lathe, internals exposed.
Scully 601 lathe at Gearbox Records in the UK.
Photo by Carl Hyde
Westrex 2B mono head, underside. 1956 diagram.
vintage 2B head purportedly owned by Capitol.
Roy DuNann recalled setting Capitol lathes up in tandem to cut multiple lacquers at the same time. This tandem method sounds brute simple (you physically bond a steel bar between the two carriages) but the practice is sophisticated. The lead-screw on the subject lathe is disengaged so the master lathe can guide both carriages; meanwhile, audio signal gets split off the upstream electronics and fed identically to two cutterheads, resulting in — theoretically — two identical lacquer cuts. Two cuts means twice the pressing capacity, which is the point: maximizing production scale from a constant x number of man-hours in the studio.
Tandem Scullys at the Capitol tower c. 1958.
Whether Contemporary took advantage of Capitol’s tandem capabilities is unclear. Perhaps for select titles. Perhaps for second and third and nth recuts but not the first cuttings. For example, popular titles would have, over time, needed fresh lacquers cut to reload metal to the pressing plant. We can plausibly imagine these re-orders were made in multiples.
Contemporary’s jacket language hints at pluralized cutting. In 1956, mastering information began appearing in the jacket technical data, in blurbs which frequently name-dropped Scully and Westrex (or Western Electric) and occasionally point to lathes and cutting heads, plural:
C3507
C3512
C3515
C3525
C5001
C3526
C3527
C3530
C3531
C3532
Lacquer “D” numbers
& Stamp Styles
(There is, by nature of the data, a lot of overlap with Reading Runouts Pt. 1 here. If you want more raw data and less narrative, I’d visit that page instead.)
“D” numbers first appeared in the runouts of Les Koenig’s records around 1954, on some 10-inch titles. These D numbers (appended by hyphen to LKL tape numbers) signified successive lacquer cuts for a program of material. For example, the third cut made from tape number LKL-18 would be LKL 18-D3.
Why Les chose the D number scheme is open to interpretation. One convincing theory suggests it was a Capitol thing, a callback to Don Lee Studios which previously occupied 5515 Melrose Ave (Meanwhile Capitol’s NYC outfit used N numbers on their lacquers). John Koenig offers a different take: that D stood for “dub,” a leftover from his father’s filmmaking roots. Both tales might have truth to them, but I’m inclined to lean the Capitol theory because 1) Capitol’s Los Angeles operation used D numbers across several labels including their own, 2) Koenig’s earliest 10- and 12-inch cuts didn’t use them.
Whatever the origin, D numbers became a permanent feature of Contemporary lacquers for the next thirty years.
It’s important to reiterate here: until at least the early 1970s, Contemporary/GTJ runout strings were imprinted into the deadwax during the plating process. This was how many labels did it in the 1950s: the cutting engineer would mark information outside of the 12-inch play area on the 14-inch lacquer disk and this information would later be machined into the lacquer deadwax by the plating firm.
That separation speaks — subtly — to the technical nature of lacquer cutting at the time. Along with that, engineers tended to be full-time label employees rather than independent contractors promoting individual sonic perspectives, so inscribing personal signatures directly in the runouts was uncommon (though the most famous jazz engineer of the day — Rudy Van Gelder — was of course doing just that).
For our purposes: Capitol’s engineers didn’t hand etch runouts, and neither did the Contemporary guys once they moved cutting in house. So the various stamp styles you see on Contemporary records usually correspond to plating plant and era and have no direct connection back to the cutting stage.
Again, for more physical detail, visit Reading Runouts Pt. 1.
DuNann’s Hand:
Tape Mastering in 1956/7
In a 1958 Down Beat profile of the bassist Mitchell brothers⁽³⁾, Red Mitchell beat the drum for Contemporary. Speaking to warmth and comfort of the recording environment at 8481, he turned his praise to the in-house engineer:
“Roy Du Nann… is certainly is one of the best in the country, and his editing and splicing is the best in town. They’re never in a hurry about editing, either. When we working on my quartet album, they gave me nine hours to edit and splice with Roy. What a good feeling it was to know you’d get what you want.” ⁽³⁾
Editing master tapes would fall more squarely under the umbrella of recording, not mastering, but I’ve included it here to build a visual: patient professional Roy DuNann works away in the control room, tapes running through his hands. This is where we’ll find him transitioning into the role of Contemporary’s mastering engineer.
C3520 Oboe/Flute
On the jacket for C3520 Oboe/Flute we find: “disk masters have been A-B'd against the master tape to insure accurate transfer.” This is (I think) the only Contemporary/GTJ jacket that bears this language, but similar messages appeared in other copy (such as the CR catalogues included with sealed records c. 1957), and it mirrors a 1956 Down Beat article by John Tynan⁽²⁾:
It may be worth speculating what this means when it for master tapes and copy tapes. As an ardent vinyl junkie, I’d urge you to not be anal about whether an LP is cut directly from master tapes or copy tapes (or a digital source, for that matter). That said—
Contemporary Records Catalogue No. 6 (1957)
The obsessive researcher in me likes to figure things out. So, in Tynan’s article⁽²⁾, DuNann has test pressings on hand while preparing an EQ’d copy tape, which implies lacquers cut prior to this step of prepping an EQ’d copy tape. Does this mean that D1 lacquers (in this period, 1955 to 1957) were cut directly from the master tapes and subsequent lacquers cut from an EQ’d copy? Or does it mean D1 was cut from a flat copy tape and those lacquers were either approved or revised by EQ’ing new cutting dupes from the masters?
DuNann and Koenig were just down the road from Capitol; it wouldn’t have been difficult to drive the master tapes there. It’s possible that Tynan here witnessed something else, perhaps the creation of a copy tape intended for shipment to the UK, where Decca cut Contemporary lacquers for distribution under the Vogue imprint.
But… what about recuts in this mid-late 50s era? If a title sold through its pressing numbers and RCA needed new metal at the plant, new Capitol lacquers would be needed. And I bet the Contemporary guys weren’t joyous about shlepping tapes back and forth over and over again if there was a more efficient solution, ie. copy tapes.
The point is, I don’t know. I’d assume all the Capitol cuts are from first-gen copy tapes, if this is a thing that matters to you. Which, again, it shouldn’t. Just listen and decide if you like how it sounds.
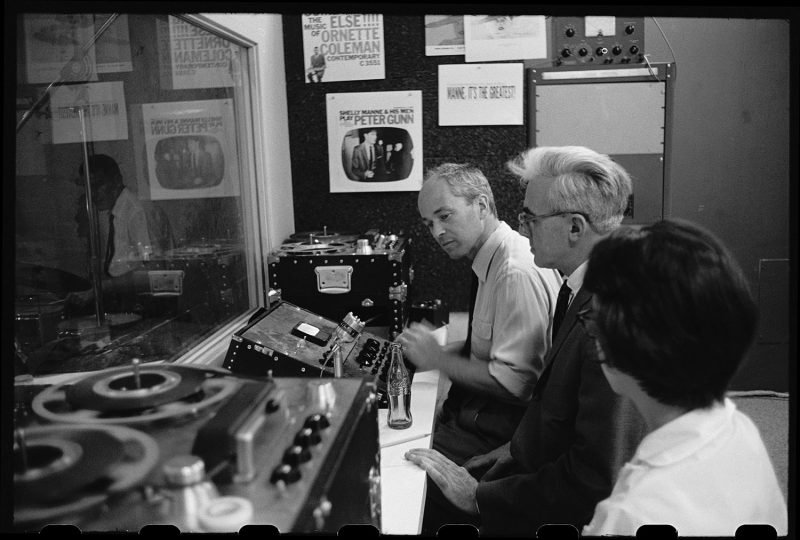

With the technical data for C3537 Double Play! comes the insertion of a new cutting lathe descriptor: “specially designed.” Small, but it marks a massive shift in strategy: the label had started cutting disc masters at 8481 Melrose.
enter Howard Holzer
Public reporting checkpoints the progression of the Contemporary lathe. As noted in The Billboard in late September 1957, Koenig hired Howard Holzer to assist DuNann in all areas, but with a specific eye to equipping the lathe.⁽⁴⁾
However it seems that the lathe was physically in-house in 1957 before Holzer’s hire was announced; the March 1958 Billboard article notes specifies a Westrex stereo cutting head in tests since “last January,” which in context should mean January 1957 but I’d wager actually refers to Jan. 1958.
Stereo cutting aside, we find vague evidence that Holzer was building the cutting room at 8481 throughout 1957. The GTJ & CR News hire announcement (October 1957) details that DuNann & Holzer had already “worked out special automatic variable pitch techniques” for the lathe.⁽⁵⁾
In Spring 1958, the lathe was announced complete — not only for cutting mono masters but also stereo.⁽⁶⁾
This was a big deal at the time. Contemporary was the first stereo cutting facility on the west coast…
…but we’re not ready to talk stereo. First we need to dissect the lathe itself.
The Contemporary &
Good Time Jazz lathe
Let’s go way back. In the 1920s, talkies arrived when Warner Bros. introduced Vitaphone. To deliver sync sound for motion pictures, a waxlike disc etched with audio would be transported to the theater and played back on a turntable in time with the film. These discs, captured on set, were cut using Western Electric lathes like those below:
A Vitaphone lathe at the Pavek Museum in St. Louis.
Western Electric D-85249 lathe (1926)
Principally similar to 1950s models such as the Scullys we saw at Capitol, the old iron Western Electric lathes lacked the style and flexibility of their gleaming midcentury successors. They were homely antiques, broken or covered in dust. Over-the-hill machines. Which meant they were pretty affordable if you happened upon one.
“In a Los Angeles junk store, Roy found a Western Electric cutting lathe that had been used on the Al Jolson film The Jazz Singer in the 1920s, and bought it for $200,” Thomas Conrad wrote.⁽¹⁾ John Koenig corroborates: “The superstructure of our lathe at Contemporary was the same lathe that the first sound movie The Jazz Singer was recorded with.”⁽⁷⁾
Now, DuNann and Holzer didn’t simply bring the old bat indoors and start using the thing. As engineers on a tight budget they knew to re-oil, modify, customize, and improvise on what they could find. The Jazz Singer bones were more than solid enough to build around them something more modern.
“It was different electronics… all of that was replaced,” John Koenig recalled.⁽⁷⁾ For example, installed was a new direct drive motor with tight tolerances that ensured — as noted in the label’s printed inner from 1962 — wow and flutter under 0.1%.
Chief among the new modifications were custom electronics to govern variable pitch:
DuNann and Holzer have worked out special automatic variable pitch techniques to accommodate the extra minutes of playing time on many GTJ & Contemporary LPs without loss of volume or bass frequency response. (GTJ & CR News, October 1957)
Variable Pitch
Pitch is the distance between two adjacent traces of a groove. Put another way, pitch is controlled by the lateral velocity which with the cutting head pushes towards the center of the disc.
Each groove modulates with a certain velocity (different velocity than in previous paragraphy), and the lateral displacement of the groove is determined by the amplitude of the monaural signal. There’s a bunch of complicated physics here, but we need only understand this: that pitch needs to be set high enough such that no two adjacent grooves touch.
From the advent of disk cutting until the 1950s, this pitch setting was kept fixed, and locked in before a cut based on running time. This didn’t allow for separate treatment of loud and quiet sections of the recording; fixed pitch was set high enough such that no section of the cut can possibly overcut into the adjacent groove.
The problem with this fixed pitch is massive amounts of wasted disc space when the program is quiet in level. So in the 1950s there arrived new tech to govern the leadscrew gear and offer variable pitch. This added to the tape machine a preview head several inches prior to the playback head; the preview signal would then feed electronics which could continuously adjust pitch in advance of the recording meeting the disk.
Studer A80 tape machine playing the Way Out West stereo master tape at Bernie Grundman Mastering in 2015. The extended physical tape path between preview and playback heads takes on various shapes depending on machine, tape speed, and tape width.
Video showing the end of a record side. As the music fades to silence, some variable pitch controllers are set to automatically create tight spirals of silent grooves before exiting to the lead-out.
Variable pitch maximizes playing time without sacrificing cutting level. Loud sections of a recording can be given a wide berth to avoid overcutting into adjacent grooves, but quieter sections with insignificant lateral modulation can be cut at very low pitch without risk.
Variable pitch has, since its introduction, been at the center of some significant shifts in mastering technique. As you can imagine, automatic motor control (as that used to create variable pitch) has grown more digital over time. Whether that means a lacquer is cut from analog or digital is a more nuanced question. In the dropdown below are the three general ways of handling automatic variable pitch in the 21st century:
-
Old-school true all-analog mastering employing two staggered tape heads (one preview and one playback). In principle the technique is unchanged since the 1950s but modern pitch controllers are often digital and quicker and more precise than their predecessors. The playback head signal continues unconverted (analog) into the analog mastering electronics. This is what we see in the Bernie Grundman tape deck picture above, and at other reputable all-analog cutting studios.
-
Alternately there exists digital delay, developed in the 1970s (by Howard Holzer no less) and widely accepted in the 1980s. This employs a single tape head whose signal gets digitized for pitch calculation then delayed a certain number of milliseconds or whatever before being fed to the cutting head. So the record itself is cut from the digital stream.
The impetus for this invention was cost and convenience. At issue with the traditional method was not the additional tape head but the need for duplicate outboard equipment to serve simultaneous preview and signal paths. So this cut studios’ investment in a declining medium (vinyl) but also freed up rack space for new cool digital shit. Remember, in the 1980s, “digital” was marketing fodder and not the dirty word it’s since become.
I’m going to go out on a limb and say this one is not a big thing anymore. Why? Think about it; digital delay is only necessary when cutting from an analog source, and any cutting engineers working with analog sources in 2023 likely care about keeping the signal analog. See your Kevin Grays, Ryan K Smiths, Bernie, lots of others. Digital delay is simply not sexy anymore.
But then you have other engineers with both feet on the digital train; they might have a tape deck but mostly use it to digitize tapes (Miles Showell, the guys at Mofi, Robert Ludwig). People who are okay with always having a digital step in the mastering chain will find more benefit from stored digital files than from running a tape source through digital delay. File storage is cheap. Which leads to the next option.
-
Mastering from a digital file. No tape machine necessary (unless the engineer is also doing the digitizing right then and there). A stored digital file gives you freedom to master in the digital realm, where there is all the time in the world. If there were issues with the original analog tape, dropouts or whatever, those are easily ameliorated in a DAW setup.
Files these days will be of higher quality than whatever format the old digital delay systems used, and they can very simply be sent in two direction with whatever latency you want… because computers are magic.
As somebody who grew up in the 90s and 2000s, I can comprehend digital pitch control. For a modern computer, pitch control is child’s play. But variable pitch was introduced in the pre-digital world and would have then been handled electromechanically. How did it work?
I don’t really know. But here’s what a couple of shirts at Westrex wrote in 1959:
The practice of altering the pitch (number of lines per inch) in standard lateral recording is now universally used as a means of obtaining maximum playing time on a phonograph record. The change in pitch is usually effected by a servomotor, which is controlled by the rectified and amplified signal from an added magnetic head spaced about 15 in. ahead of the normal reproduce head in the tape machine supplying stereo signals to the disc recorder.
— Recent Developments in Stereo Disk Recording, Frayne & Davis, Feb. 1959⁽⁸⁾
Another responsibility of this “servomotor” or whateveritwas was the automatic creation of the lead-out groove. Which is going to be important in a moment.
Finding the 8481 Melrose cuts
Let's recap the chronology. Holzer’s hire was announced in Fall 1957 — though it may have happened earlier that year — and the lathe was up and running at 8481.
So how does this square with the titles released in this period? Do we know when exactly mastering shifted to the new system at 8481 Melrose?
We can use the GTJ & CR News for release timing; this was a newsletter mailed directly from the label with routine previews of upcoming albums (and other label-adjacent stories). The News albums announcements came close before street date and were usually paired with artwork mockups, track listings, and quotes pulled from the liner notes.
Titles C3535 to C3544 first appeared in the News in late 1957 — and it’s in this stretch we see the jacket technical data shift its language to reflect the “specially-designed” lathe at 8481.

C3535 retains Capitol language: “Scully…”

C3537 adds “specially designed…”
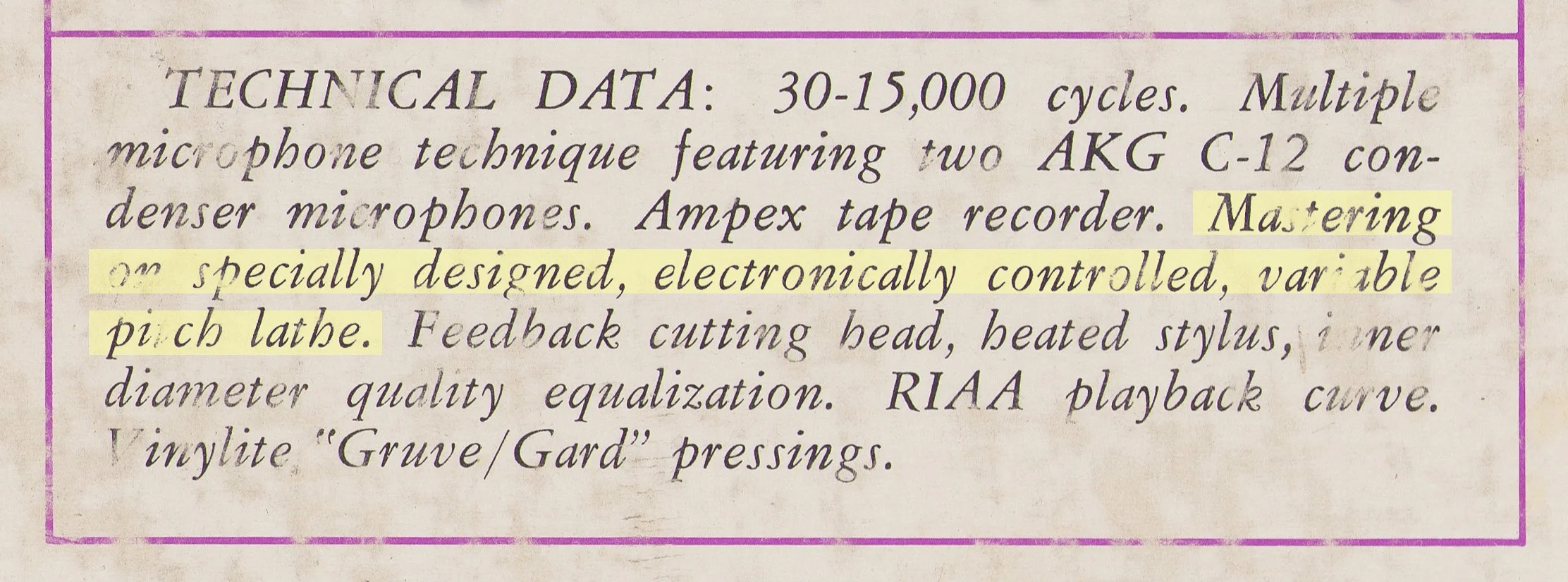
C3539 offers the same lathe description…
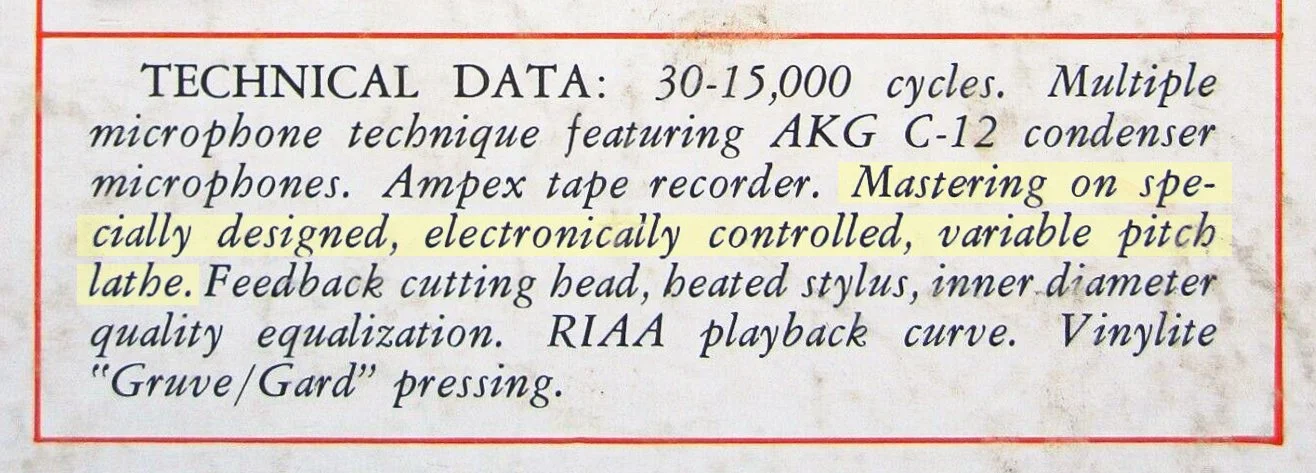
C3543. Same thing.
Examining the Technical Data… gets us only so far
So C3537 was the first title to include “specially designed” in its lathe language. C3538, 39, 40, 42, 43, and 44 repeat it.
So what can we infer about mastering for all of these titles? We might read that Contemporary broke from Capitol after C3535 or C3536 such that every title after this was mastered on the “specially designed” lathe at Contemporary.
But we can not blindly trust printed jacket details. We need to treat the printed technical data as marketing language that speaks to timing and chronology, but NOT as evidence for the specific record inside each jacket. The jackets express the latest mastering techniques favored by the label, not the mastering technique specifically used for each title.
The changes in jacket language point directly to the real belief that the lathe was ready, or even in partial use by late 1957. And while the sudden inclusion of “specially designed” on C3537 should specify mastering on the 8481 Melrose lathe, the physical data disagrees, and suggests a more staggered truth. We’ll find that truth in the lead-out grooves.
Lead-out Grooves, Pt I:
Ye olde eccentric.
The playback experience with a mid-1950s LP is not so different than any record off the shelf today. Maybe you hit the mono button on your modern phono preamp, but otherwise no sweat. That backwards compatibility is part of what makes vinyl feel eternal.
But when the music stops, things can take a frightening turn. Abruptly your needle can be jerked inwards; you look up to find the tonearm whiplashing across the deadwax like a ragdoll, scratching and popping as if cutting across paper. You rush to your system’s rescue to save your wallet from certain disaster.
Rest easy, little hobbit. This oddity of the past is startling but harmless, and we call it an eccentric lead-out groove, or eccentric shut off, or another variation of this. You could also call this an off-center lock groove, or the big whiplash, or the super duper swervy thing. It doesn't matter so long as we all know what it is we're talking about.
C3525, early pressing with eccentric lead-out
Later cut with concentric lead-out. Note identical labels.
These are the two variants on the conclusion of a record side, where the playback stylus pulls closest to the center of the disk and rests there until either a) you come collect it or b) an automatic stop function pulls it back to the armrest.
The history of these lead-outs was about user experience and technological necessity. Eccentric grooves were cut into 78s as early as the 1920s as a trigger for the stop function on automatic changers of the day. These changers sense the tonearm moving inwards then back outwards to trigger the stop; thus the rapid back-forth of the eccentric lead-out.⁹
Early LP auto-changers adopted this same "eccentric trip" mechanism as their 78 brethren, but in the 1950s a new style of mixed-format changer emerged and changed the status quo. Mastering engineer Thomas Daly posted about this several years ago on the Steve Hoffman forum (bolding mine):
In the early 1950s, The Voice of Music devised a multi-speed record changer called the "Tri-O-Matic," that could not only play any of the three speeds of record, but could also intermix 10" and 12" records (but not 7"). This changer could also power itself off after all of the records played. The Tri-O-Matic also introduced a new trip mechanism, required because 45s weren't designed with eccentric lead-out grooves. The Voice of Music's new changer used what was called "velocity trip," as the tone-arm moves faster toward the record label as the stylus traces the lead-out grooves. Velocity trip has been used in most multi-speed record changers since 1955, eliminating the need for eccentric lead-out grooves, and is still used today in semi-automatic turntables to trigger the auto-stop. (source: Thomas Daly)⁽⁹⁾
Beautiful.
So how exactly were these lead-outs made? The original eccentric groove needed to be cut separately from the rest of the groove, which arcs concentric to the center hole. The cutterhead would thus cut a groove arcing towards the center at which point it would be abruptly lifted from the lacquer, leaving the groove unfinished.
An eccentric circle would then by cut such that it intersected with the existing groove at the lift point. This could be done in one of a couple ways. 1) the lacquer could be taken off the lathe and placed on a separate turntable dedicated to cutting the eccentric. Alternately 2) the lacquer could be mounted with an off-center clamp, then a special cutting jig brought over the disc and hinged to a fulcrum to the side on the platter. This cutter would run flush against the off-center clamp such that spinning the platter resulted in a circle 1/8" off-center. Maybe there were additional methods.
The second method can be seen in this video, captured at History of Recorded Sound in Culver City. Here resident engineer and well-known west coast audioman Len Horowitz cuts an eccentric lead-out for a 78rpm cut:
However it was cut, the eccentric lead-out was probably a pain in the ass for the engineer. So, once no longer needed on the consumer end, the eccentric lead-out quickly gave way to a CONCENTRIC lead-out, ie. the “stationary” lock groove we know and love and which the Beatles and prog bands cut their audio tricks into.
Lead-out Grooves, Pt II:
8481 goes Concentric.
Creation of a concentric lead-out is simple. Or at least simpler than the alternative.
It allows the main cutterhead to work uninterrupted all the way through the end of the side. Less fuss and fewer cock ups, because automation: the same electronics that govern variable pitch can calculate and complete the lead-out groove without human intervention. It’s just a lot easier.
Cutting the concentric lead-out groove. Video shows a Neumann lathe and cutterhead finish a (10-inch?) side, automatically cut the lead-out, lift off the disk, then return to start.
Every Contemporary LP cut before 1957 has the eccentric lead-out groove... and somewhere in 1957 that eccentric lead-out starts to flicker away before 1958 kills it forever.
Which is valuable data to us, because it signifies more than just evolving technology: Capitol in LA seems to have continued cutting concentric grooves in their 12” lacquers until 1960.⁽¹⁰⁾
So the change in lead-out groove style we witness in 1957/1958 *likely* signifies the move from Capitol’s cutting room to Contemporary’s. Meaning:
every mono lacquer with an eccentric lead-out groove was cut at Capitol.
every mono lacquer with a concentric lead-out (up to 1980) was cut at Contemporary.
Let’s look specifically at an early Good Time Jazz title, L-12012 The Firehouse Five Story, Vol. 3. This was a 12-inch reissue of 10-inch title L-16 (1953) and first released in 1955. The original 12-inch release has specific language that speaks (vaguely) to new mastering techniques used to spruce up the old recordings. And it provides the date of remastering, October 1955. So, at Capitol.
A few years later the title was reissued with largely identical designs but for two notable changes. These were new lacquer cuts with concentric lead-outs (unlike the eccentric lead-outs on the 1955). Corresponding to that, there is a new date listed on the jacket for the (re-)remaster: January 1958:
L-12012, 1955 original
L-12012, 1958 reissue
Love it. So let’s see if this principle can apply to the late 1957 stretch of Contemporary titles. Charted below is the stretch of CR titles we’ve been discussing and the lead-out style on the earliest production lacquers (ie. first pressings). Depending on eccentric or concentric lead-out, we can theorize whether they were first cut at Capitol or at 8481:
A data concern here. It’s not always simple to confirm a pressing is a first pressing if it has concentric lead-outs. We don’t have data on every lacquer that was cut or attempted, and some didn’t make it past test pressings. If a D1 lacquer appears on either side of a sample LP we can easily confirm it’s the earliest variant and deduce where the original lacquers were cut. However if the lowest we find on either side is D2 or above, we need to use jackets and sample size and other identifiers and this quickly gets less definitive. In particular, I’m concerned about a title like C3544, recorded in 1957, tape assembled quickly… but the earliest seems to be the concentric D2/D2 cuts. It’s very possible it had D1 lacquers cut at Capitol and not used for pressing. Or not; the D1 cuts might have been Contemporary attempts.
Consider that the early stages of the in-house Contemporary cutting operation were highly experimental, meaning many of their first attempts at a title would have been scrapped or blown or rejected. So there is much we don’t know; some educated guesswork is involved and we have to roll with that.
Mixed lead-out pressings? Possibly non-existent. I’ve seen a lot of mono pressings from the C3501-47 range (47 is the last eccentric, far as I can tell), and while there are numerous examples of eccentric originals versus concentric reissues, I’ve not seen any pressings with mixed lead-outs (ie. eccentric on one side and concentric on the other). Perhaps Contemporary/GTJ voluntarily chose to recut both sides of an album even if just one side of metal got blown. To think about why: this would create more consistent sonic signature between the two sides; a Capitol cut on one side and 8481 Melrose cut on the other might yield different levels and tone between the two.
All that said, it’s entirely possible that mixed lead-out pressings are out there. Maybe you have one. I’d specifically look to a big seller like C3527 My Fair Lady for an example, should it exist.
Sidebar… What about Lead-IN Grooves??
The lead-in grooves start the disc. You know, those lines that catch the needle before the music starts.
I wanted to study them. Measuring LPI (lines per inch) of the lead-in seemed like it would be fun, and I entertained diving deep into that data… but I did a pretty quick about-face. Measuring LPI is fiddly as hell. I don’t think I have the tools. Close to a record surface is no place for sharp metal calipers.
Lead-in grooves.
For completeness, though, I did glean something from these lead-ins. Capitol's tandem Scully lathes were known to cut them at a dependable 32 LPI (source), which was one of the standard factory settings for the Scully. This gels with what I’ve seen on any 12-inch Contemporary/GTJ lacquers before 1957.
And here’s what I witnessed in the 1957/1958 titles: immediately with C3541 Suite Sixteen! the lead-in LPIs on Contemporary lacquers start varying cut to cut. However this variance only occurs on the lacquers with concentric lead-outs. Lacquers with eccentric lead-outs never stray from the Scully-esque 32-pitch. The lead-in LPIs on concentric lead-out cuts vary a lot… almost like they were cut using new electronics still being fine tuned.
When cross-referenced against eccentric lead-outs, lead-in LPI data adds further support for the eccentric lead-out as a giveaway for a Capitol cut, and its eschewal as indication of Contemporary taking the reins.
The story continues in Vol. 2 >>
Sources
Acoustic Sounds. “An Interview with John Koenig, Former President of Contemporary Records.” YouTube, YouTube Video, 22 Apr. 2022, www.youtube.com/watch?v=GAsuVLN_lyo. Accessed 2022.
Boden, Larry. Basic Disc Mastering. 1978. 3rd ed., 2022.
Jazz Discography Project. “Contemporary Records Discography Project.” Jazz Discography Project, www.jazzdisco.org/contemporary-records/. Accessed 2020.
(1) Conrad, Thomas. “The Search for Roy DuNann.” Stereophile.com, Apr. 2002, www.stereophile.com/interviews/402roy/index.html. Accessed 2020.
(2) Tynan, John. “Contemporary Started as Classics Label.” Down Beat, vol. 23, no. 21, Oct. 1956, p. 14. Internet Archive.
(3) “The Red and Whitey Blues.” Down Beat, vol. 25, no. 11, May 1958, pp. 18–19, 45–46. Internet Archive.
(4) “Holzer to GTJ as Technician.” The Billboard, 30 Sept. 1957, p. 26. Google Books.
(5) “Holzer to GTJ.” GTJ & CR News, vol. 2, no. 4, Oct. 1957, p. 3. Retrospective Index to Music Periodicals.
(6) “Contemporary Signs Hentoff to A&R Pact.” The Billboard, 31 Mar. 1958, p. 5.
(7) “The John Koenig Interview.” YouTube, YouTube Video, 9 Apr. 2023, youtu.be/yNM-YR6Afy4?t=4565. Accessed 2023.
(8) Frayne, John G., and R. R. Davis. “Recent Developments in Stereo Disc Recording.” Journal of the Audio Engineering Society, vol. 7, no. 4, Audio Engineering Society, Oct. 1959, pp. 147–52, 180. Accessed 2023.
(9) Daly, Thomas. Comment on “Eccentric Run-Out Record Grooves.” Steve Hoffman Music Forums, 10 Jan. 2015, https://forums.stevehoffman.tv/threads/eccentric-run-out-record-grooves.130718/page-2#post-11671684.
(10) W.B. Comment on “Eccentric Run-Out Record Grooves.” Steve Hoffman Music Forums, 2 Nov. 2007, https://forums.stevehoffman.tv/threads/eccentric-run-out-record-grooves.130718/#post-2993707.